5.3 Prefabrication and Modular Construction
Prefabrication and modular construction methods have revolutionized the construction industry, offering efficient, cost-effective solutions for building Accessory Dwelling Units (ADUs). By leveraging off-site construction, prefabricated ADUs streamline the building process, reduce labor costs, minimize material waste, and significantly shorten project timelines. This guide provides insights into how ADU companies can use prefabrication and modular designs to their advantage, covering the entire process from planning to completion.
Why It Matters
Prefabrication and modular construction streamline the ADU building process by leveraging off-site production for faster timelines, reduced labor costs, and consistent quality. These methods are ideal for meeting the rising demand for cost-effective and efficient ADU solutions.
Key Highlights
- What is Prefabrication?
- Prefabrication involves manufacturing building components (walls, floors, roofs) in a factory-controlled environment, then assembling them on-site.
- Reduces on-site labor, enhances precision, and minimizes waste.
- What is Modular Construction?
- Modular construction builds entire sections or modules (e.g., kitchens or bathrooms) off-site, ready for quick assembly at the site.
- Scalable, efficient, and suited for both small and large ADU projects.
- Benefits of Prefabrication and Modular Construction
- Faster Timelines: Construction time reduced by 30–50% due to parallel on-site preparation and off-site module building.
- Cost Savings: Lower labor costs and reduced waste.
- Enhanced Quality Control: Factory-built components meet high standards and minimize errors.
- Sustainability: Less material waste and eco-friendly features, such as energy-efficient systems, can be integrated during production.
- Process Overview
- Design and Customization: Clients select modular designs with optional customizations.
- Permitting and Site Prep: Simultaneous factory production and site preparation (foundation, utilities).
- Manufacturing: Modules built in 4–8 weeks in a controlled environment.
- On-Site Assembly: Modules craned into place, utilities connected, and final touches added.
- Cost Considerations
- Lower labor and manufacturing costs, but site preparation and transportation expenses may vary.
- Long-term savings from energy-efficient construction and reduced maintenance.
- Challenges
- Limited customization compared to traditional builds.
- Transportation logistics for oversized modules may require special permits and equipment.
Toolbox Ideas
- Prefabrication vs. Traditional Construction Comparison Chart
- Visual guide to help clients and builders understand the pros and cons of each method.
- Visual guide to help clients and builders understand the pros and cons of each method.
1. Understanding Prefabrication and Modular Construction
a. What is Prefabrication?
Prefabrication refers to the process of manufacturing building components—such as walls, floors, or roofs—off-site in a factory-controlled environment. Once the components are built, they are transported to the construction site and assembled.
Key Features:
- Factory-built components: Building elements are produced in a factory and transported to the site.
- Less on-site labor: The bulk of the construction happens off-site, reducing the time and labor needed on-site.
- High precision: Controlled factory environments allow for higher quality control and precision during fabrication.
b. What is Modular Construction?
Modular construction is a form of prefabrication in which entire sections or modules of the ADU are built off-site and then transported to the site for assembly. These modules can include fully finished sections like rooms, kitchens, or bathrooms.
Key Features:
- Pre-built modules: Fully or partially finished units (e.g., kitchen or bathroom) are assembled off-site.
- Quick assembly on-site: Modules are quickly assembled on-site to form the ADU.
- Scalable: Modular units are scalable, making them ideal for both small and large ADU projects.
2. Advantages of Prefabricated and Modular ADUs
a. Speeding Up Construction Timelines
One of the most significant advantages of prefabrication and modular construction is the shortened build time. Prefabrication can cut construction time by 30-50%, depending on the project size and complexity.
How It Speeds Up Construction:
- Concurrent processes: While the ADU components are being built in the factory, the foundation and site preparation work can happen simultaneously, leading to parallel construction phases.
- Reduced weather delays: Since most of the construction happens in a controlled factory environment, weather delays that typically affect traditional construction are minimized.
- Faster assembly: Pre-built modules are delivered and installed in a matter of days, significantly speeding up the overall timeline.
b. Lower Labor Costs
Because most of the labor-intensive work is done in the factory, fewer workers are needed on-site. This can reduce labor costs by 10-20%.
Key Cost-Saving Benefits:
- Efficient labor use: Factory-based labor is typically more efficient and less costly than hiring a full construction crew on-site for extended periods.
- Reduced on-site duration: A shorter on-site construction timeline means fewer hours paid to local workers for assembly and finishing.
c. Enhanced Quality Control
Factory environments offer better control over the quality of materials and the building process, leading to higher construction precision and fewer errors.
Quality Advantages:
- Consistent standards: Factory-built components are manufactured under strict quality standards, ensuring that each part of the ADU meets regulatory codes.
- Reduced material waste: Factories use optimized processes that reduce material waste, which in turn lowers costs.
d. Sustainability and Reduced Waste
Prefabrication and modular methods can make ADUs more sustainable by minimizing waste and using energy-efficient manufacturing processes.
Environmental Benefits:
- Less material waste: Prefabrication uses exact quantities of materials, reducing the amount of waste produced during construction.
- Energy efficiency: Modular construction often includes eco-friendly features like energy-efficient windows, insulation, and solar panels, which can be added in the factory.
3. The Process of Building a Prefabricated or Modular ADU
a. Initial Consultation and Design
The process begins with an initial consultation where clients select a prefabricated or modular ADU design that fits their needs.
Steps:
- Needs assessment: Determine the client’s goals, such as size, layout, and features of the ADU.
- Design selection: Choose a pre-approved or custom modular ADU design from a catalog.
- Customization options: Depending on the manufacturer, some customization in layout, finishes, and exterior design may be available.
b. Permitting and Site Preparation
Once the design is finalized, permits must be obtained from the local government. At the same time, site preparation, such as foundation work, can begin.
Steps:
- Submit permits: Work with local authorities to secure all necessary permits for ADU construction.
- Prepare the site: Clear the site, install utilities (water, sewage, electricity), and lay the foundation (usually a concrete slab).
- Coordinate with factory: Communicate with the factory to ensure the ADU modules are built to the agreed specifications while the site is being prepared.
c. Manufacturing the ADU
The modular units or prefabricated components are built in a controlled factory environment. This stage usually takes 4-8 weeks, depending on the complexity of the ADU.
Key Factory Processes:
- Module construction: Walls, floors, ceilings, and other components are built and fitted with plumbing, electrical, and HVAC systems as needed.
- Quality control: The units undergo rigorous inspections to ensure they meet building codes and quality standards.
- Transportation: Once completed, the modules or components are transported to the construction site.
d. On-Site Assembly and Installation
Once the modules or prefabricated components arrive at the site, the on-site assembly begins. This stage is significantly faster than traditional construction.
Steps:
- Craning and installation: Modules are craned into place and assembled on the foundation. Prefabricated components are fitted together on-site.
- Utility connections: The ADU’s plumbing, electrical, and HVAC systems are connected to the site’s utilities.
- Finishing touches: Final touches like painting, flooring, and landscaping are completed.
- Final inspections: A final inspection is conducted by local authorities to ensure the ADU meets all safety and building regulations.
e. Client Handover
Once the ADU is fully assembled, inspected, and approved, it is ready for handover to the client. Provide the client with necessary documentation, including warranties, maintenance guides, and user manuals for any installed systems.
4. Cost Considerations for Prefabricated and Modular ADUs
While modular construction is generally more cost-effective than traditional building methods, there are specific factors to consider when budgeting for a prefabricated or modular ADU:
a. Upfront Costs
- Factory manufacturing: This includes the cost of producing the modules or components, which is typically lower than traditional construction labor costs.
- Transportation: Depending on the location of the factory, transporting the modules to the site can add to costs, particularly if the site is far from the factory.
- Foundation and site work: Even with prefabricated units, site preparation and foundation work are still required, which can vary depending on the condition of the site.
b. Long-Term Savings
Prefabricated ADUs often result in long-term savings:
- Energy efficiency: Modular ADUs are often built with energy-efficient materials, reducing energy bills over time.
- Lower maintenance: Factory-built units tend to have fewer structural issues, which reduces long-term maintenance costs.
5. Challenges and Limitations
While prefabrication and modular construction offer numerous advantages, there are some challenges to consider:
a. Limited Customization
- Design constraints: While modular designs offer some flexibility, fully custom designs may not always be feasible within the modular framework.
- Exterior aesthetics: Some clients may prefer traditional construction for more intricate architectural features.
b. Transportation Logistics
- Transport restrictions: Oversized modules may require special permits for transport, and there could be additional costs if cranes or other heavy equipment are needed to assemble the units on-site.
6. Conclusion: Prefabrication and Modular Construction as the Future of ADU Building
Prefabricated and modular construction methods offer an efficient and cost-effective solution for ADU projects. By reducing on-site labor, speeding up timelines, and offering more consistent quality control, these methods are well-suited to meet the growing demand for ADUs in urban and suburban areas. While there are limitations in customization and transportation logistics, the benefits far outweigh the drawbacks, making modular construction an ideal choice for builders looking to scale their operations and clients seeking affordable, high-quality housing solutions.
By adopting these innovative methods, ADU companies can streamline their project management, enhance client satisfaction, and increase profitability.
Up next
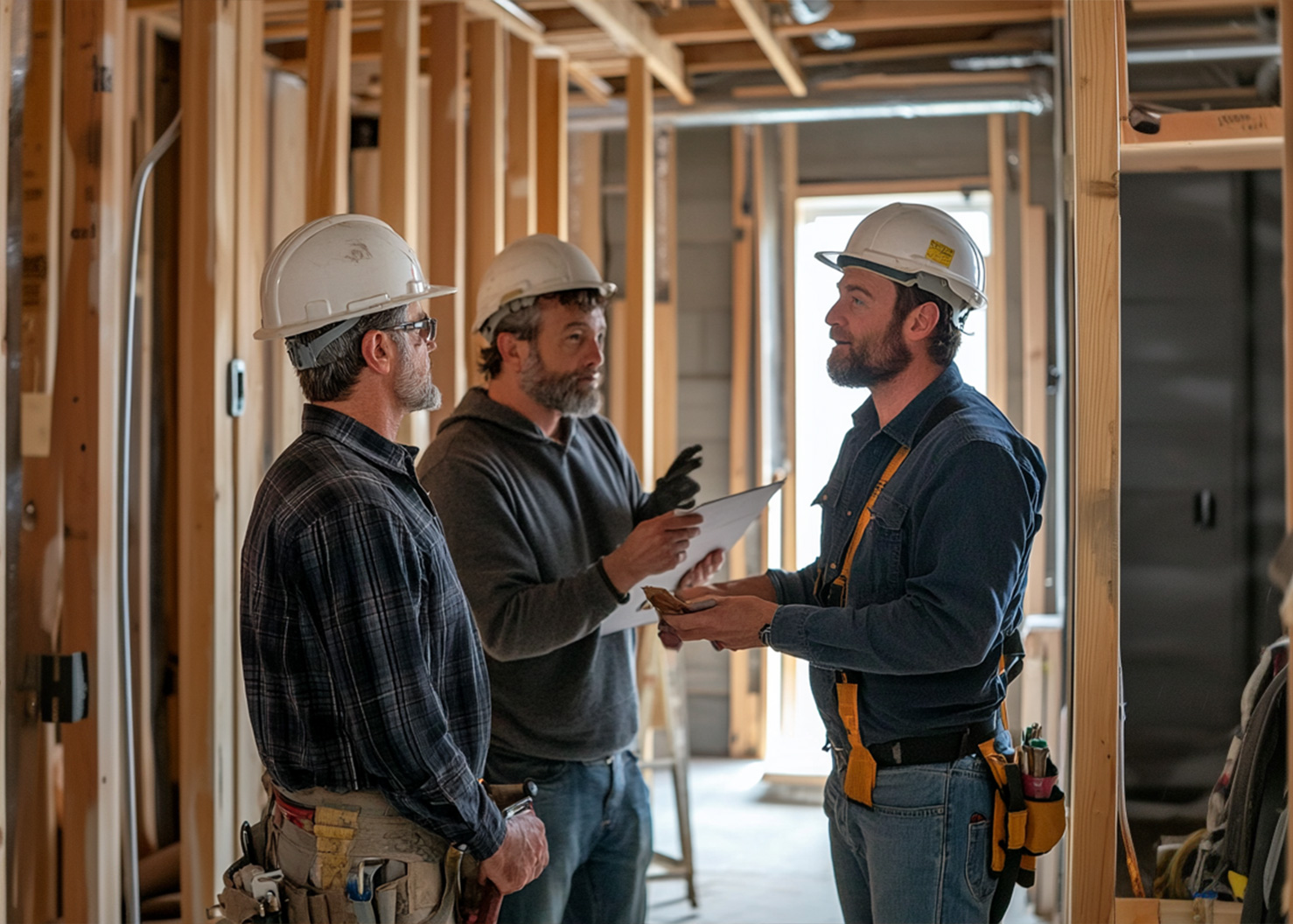